In the field of machinery, bevel gear as a commonly used transmission elements, with simple structure, smooth transmission, low noise and other advantages. However, in the process of production and use, the surface quality of bevel gears directly affects their transmission efficiency and service life. Therefore, the polishing process of bevel gears is particularly important. In this paper, we will discuss the technical points of bevel gear polishing, equipment selection, operation steps, etc., in order to provide reference for relevant personnel.
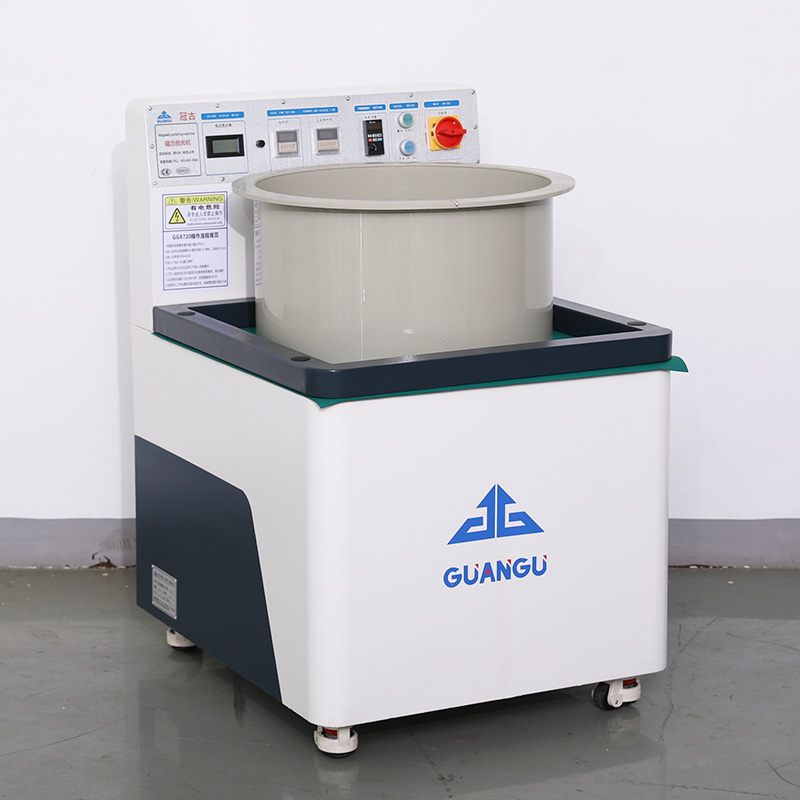
First, the technical points of polishing
- Bevel gear surface quality: the purpose of polishing is to improve the surface quality of the bevel gear, reduce surface roughness, in order to reduce the coefficient of friction, improve transmission efficiency. Surface quality mainly includes Ra, Rz and other parameters, these parameters affect the bevel gear friction, wear and noise and other properties.
- Polishing process: gear polishing process includes hand polishing and mechanical polishing. Hand polishing is mainly applicable to small batch, high-precision requirements of the bevel gear, while mechanical polishing is suitable for mass production. Mechanical polishing can be divided into dry polishing and wet polishing, dry polishing is suitable for bevel gears with high hardness, wet polishing is suitable for bevel gears with low hardness.
- Polishing materials: the choice of polishing materials is crucial to the polishing effect of bevel gears. Commonly used polishing materials are polishing wheel, polishing belt, polishing liquid and so on. Polishing wheel and polishing belt for hard gear polishing, and polishing liquid is suitable for soft gear polishing.
Second, bevel gear polishing equipment selection
- Manual polishing equipment: manual polishing mainly depends on the polishing wheel, polishing belt and other tools, as well as polishing machine, rotary table and other auxiliary equipment. Polishing machine can be divided into electric polishing machine and pneumatic polishing machine, according to the size and shape of the bevel gear to choose the right polishing machine.
- Mechanical polishing equipment: mechanical polishing equipment mainly includes polishing machines, polishing wheels, polishing belts, polishing fluid and so on. Polishing machine has dry polishing machine and wet polishing machine two kinds, according to the bevel gear material and surface requirements to choose the right polishing machine.
Third, gear polishing operation steps
- Pre-treatment: bevel gear clean, remove surface oil, rust and other debris. For hard bevel gear, can use sandblasting, deburring and other methods of pretreatment.
- Hand polishing: place the bevel gear on the rotating table, and use the polishing wheel or polishing belt for hand polishing. In the process of manual polishing, we should ensure that the uniform pressure of the polishing wheel or polishing belt to avoid scratches.
- Mechanical polishing: place the bevel gear on the polishing machine, choose the appropriate polishing wheel, polishing belt and polishing liquid. Mechanical polishing process, pay attention to the polishing speed, pressure and concentration of polishing liquid and other parameters to ensure the polishing effect.
- Inspection and acceptance: After the polishing is completed, the surface quality of the bevel gear is inspected to confirm whether the desired effect is achieved. If necessary, the second polishing or repair.
In short, gear polishing process is important for improving transmission efficiency and aesthetics. Through the selection of appropriate polishing equipment and technology, in strict accordance with the operating steps for polishing, can ensure that the surface quality of bevel gears to meet the expected requirements. In the actual production process, according to the bevel gear material, size and surface requirements, flexible adjustment of polishing parameters to achieve the best polishing effect.
You must be logged in to post a comment.