With the rapid development of science and technology, flying cars are gradually moving from science fiction movies to real life. As an emerging means of transportation, flying cars integrate advanced technologies in multiple fields such as aerospace, automobiles, and electronics. Driven by my country’s policy support and market demand, the flying car industry is ushering in unprecedented development opportunities. However, in the processing of flying car parts, the precision requirement is extremely high, which poses a severe challenge to the manufacturing process. As an efficient and precise processing equipment, the magnetic polishing machine plays an important role in the manufacturing of flying car parts.Magnetic polishing machine helps the surface treatment of flying car parts.
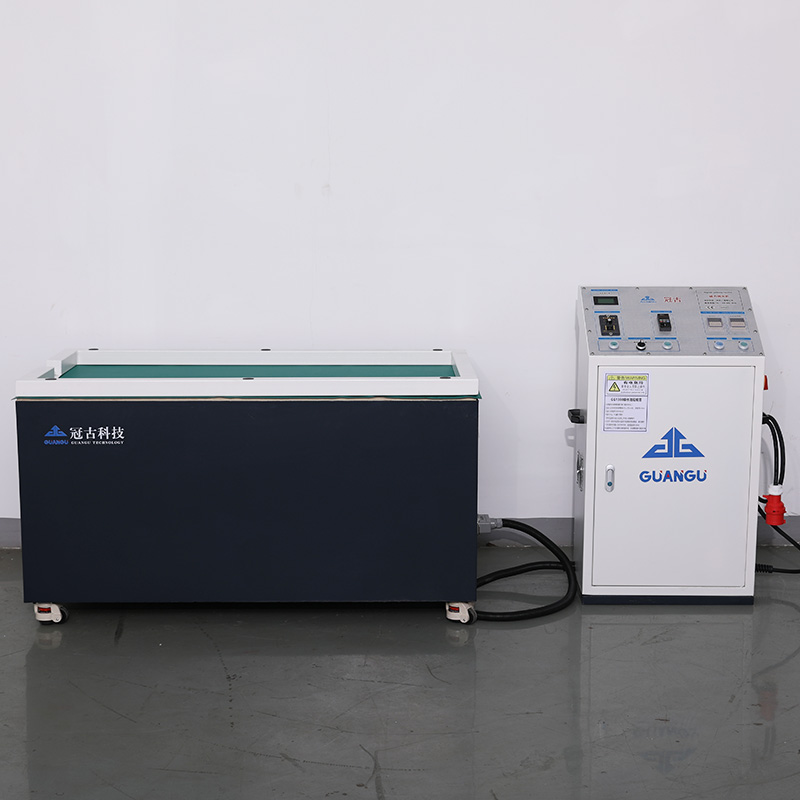
1. Challenges faced by flying car parts processing-Magnetic polishing machine helps the surface treatment
Complex structure: Flying car parts have complex structures and changeable shapes, and traditional processing methods are difficult to meet their precision requirements.
High precision: During the flight of flying cars, the precision requirements of parts are extremely high, and a slight deviation may lead to flight accidents.
Material diversity: Flying car parts involve a variety of materials, such as aluminum alloys, titanium alloys, composite materials, etc., which put forward different requirements for processing technology.
Surface quality: The surface quality of flying car parts directly affects its service life and flight performance, and high-quality surface treatment technology is essential.
2. Application of magnetic polishing machine in flying car parts processing
Precision processing: The magnetic polishing machine uses the magnetic field to make the polishing medium (various types of grinding steel needles) grind the parts evenly and finely, effectively improving the precision of the parts.
Applicable to complex structures: The magnetic polishing machine can customize the magnetic field distribution according to the shape and size of the parts to achieve precision processing of complex structures.
Strong material adaptability: The magnetic polishing machine can be applied to a variety of materials to meet the material diversity requirements of flying car parts.
Excellent surface quality: The surface of the parts processed by the magnetic polishing machine is smooth and flat, which effectively improves the service life and flight performance of the parts.
High efficiency: The magnetic polishing machine adopts automatic control, with high processing efficiency and shortened production cycle.
Environmental protection and energy saving: The magnetic polishing machine uses water-based polishing liquid to reduce pollution to the environment, which is in line with the concept of green manufacturing.
3. Advantages of magnetic polishing machine in flying car parts processing
Improve processing accuracy: The magnetic polishing machine can achieve high-precision processing of flying car parts and ensure the quality of parts.
Optimize processing process: The magnetic polishing machine simplifies the processing process of flying car parts and reduces production costs.
Improve product competitiveness: Flying car parts processed by magnetic polishing machines have obvious advantages in precision and surface quality, which improves product competitiveness.
Meet personalized needs: Magnetic polishing machines can be customized according to the characteristics of different parts to meet the personalized needs of flying car parts.
In short, magnetic polishing machines have significant advantages in the processing of flying car parts, providing strong support for the development of my country’s flying car industry. With the continuous optimization and upgrading of magnetic polishing technology, it is believed that in the near future, magnetic polishing machines will play an important role in more fields and help my country’s manufacturing industry move to a higher level.
You must be logged in to post a comment.