With the development of science and technology, aluminum alloy, as a lightweight and high-strength material, has been widely used in many fields. However, the surface quality of aluminum alloy parts has an important impact on their performance and life. In order to meet the requirements of high precision and high finish, magnetic polishing technology has been gradually introduced into the machining process of aluminum parts. In this paper, the principles, applications and economic considerations of magnetic polishing of aluminum alloy parts will be discussed in depth.
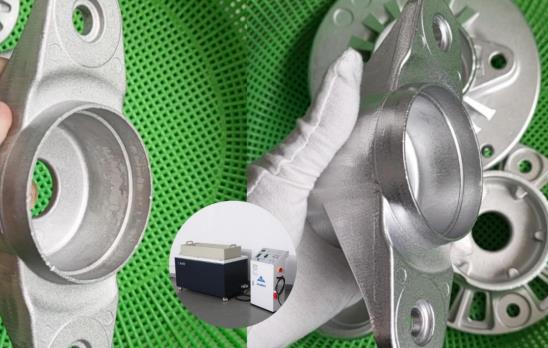
The nature and processing requirements of aluminum alloy
Aluminum alloy is mainly composed of aluminum and other alloying elements, such as copper, magnesium, zinc and so on. Different combinations of these elements can affect the strength, hardness, corrosion resistance and machining properties of aluminum alloys. During machining, the surface quality of aluminum alloy parts is easily affected by material hardness, toughness and tool wear. Therefore, improving the surface quality of aluminum parts is essential to meet industrial demands.
Principle of Magnetic Polishing Technology
Magnetic polishing uses a magnetic field to drive the abrasive grains to slide on the surface of the workpiece, thus realizing the grinding and polishing of the surface of the workpiece. The abrasive grains are magnetized under the action of the magnetic field and are driven by the magnetic field force to move along the magnetic line of force. Due to the non-uniformity of the magnetic field, the abrasive grains will produce irregular movement on the surface of the workpiece, thus realizing the fine grinding and polishing of the workpiece surface.
The implementation process of magnetic polishing of aluminum alloy parts
The implementation of polishing of aluminum alloy parts needs to go through the following steps: firstly, select the appropriate magnetic polishing equipment and magnetic abrasive grains; secondly, carry out preparatory treatment for aluminum parts, including cleaning, deburring, etc.; finally, place the aluminum alloy parts in the working area of the magnetic polishing equipment, and adjust the parameters of the magnetic field and the type of abrasive grains to achieve the best polishing effect.
Effect and influence of magnetic polishing
The effect of magnetic polishing on the surface quality of aluminum parts is mainly reflected in the improvement of surface finish and reduction of surface roughness. The surface of aluminum alloy parts after magnetic polishing can obtain micro-scale roughness, thus improving the corrosion resistance and mechanical properties of the parts surface. In addition, magnetic polishing can also enhance the fatigue resistance of aluminum parts to extend their service life.
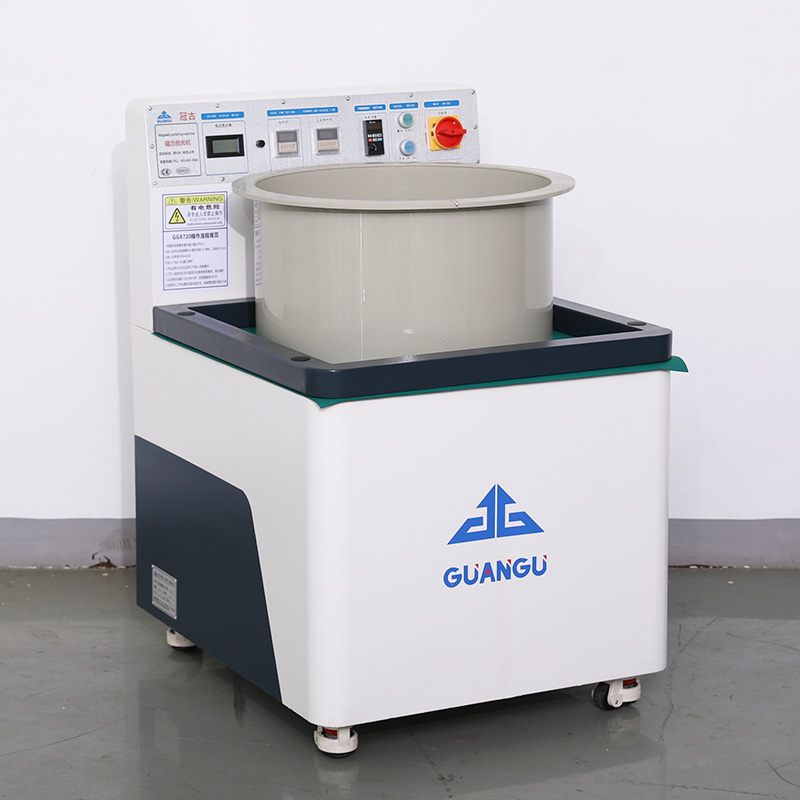
Practical application cases-Magnetic Polishing of Aluminum Alloy Parts
Magnetic polishing of aluminum alloy auto parts is one of the typical application cases. The demand for light weight and lower manufacturing cost in the automobile manufacturing industry has driven the application of aluminum alloy in automobile parts. Through magnetic polishing technology, the surface quality of aluminum alloy automotive parts can be significantly improved, reducing friction resistance and improving fuel efficiency.
Magnetic polishing of aluminum alloy aerospace parts is also an important application area. The aviation industry has extremely strict requirements on the quality and performance of materials, and aluminum alloy, as a kind of lightweight and high-strength material, is suitable for aviation structural parts and internal parts. Through magnetic polishing technology, a high quality surface condition can be obtained, improving the corrosion resistance and mechanical stability of aerospace parts.
Technical and economic considerations
From the technical and economic point of view, magnetic polishing technology has the following advantages: firstly, magnetic polishing can be carried out at room temperature, avoiding the high temperature and high-pressure environment in the traditional mechanical polishing process, reducing energy consumption and equipment costs; secondly, the processing cycle of magnetic polishing is short, and the productivity is high, so that mass production can be realized; in addition, magnetic polishing can also realize the local polishing of workpieces to meet specific surface High-precision processing needs. Therefore, magnetic polishing technology has high economic feasibility, especially suitable for the aluminum parts manufacturing field with high requirements on surface quality.
Conclusion-Magnetic Polishing of Aluminum Alloy Parts
The principle, application and economic consideration of magnetic polishing technology for aluminum alloy parts show its important position in the industrial manufacturing field. Through magnetic polishing technology, the surface quality of aluminum parts can be improved, the manufacturing cost can be reduced, and the market competitiveness of products can be improved. With the continuous development of science and technology, it is believed that the application areas of magnetic polishing technology for aluminum parts will be further expanded in the future, bringing more possibilities for industrial manufacturing.
You must be logged in to post a comment.