Why should we conduct sample testing before purchasing a magnetic polisher?
In industrial production, magnetic polishers are widely used in deburring, polishing, cleaning and other processes in metal parts, precision instruments, medical devices, jewelry and other fields as an efficient and environmentally friendly surface treatment equipment. However, improper equipment selection may lead to low production efficiency, cost waste and even product quality problems. Therefore, it is a crucial step to conduct sample testing (i.e. verifying the performance of the equipment through actual samples) before formal purchase. The following analyzes its necessity from multiple dimensions.
- Verify the compatibility of equipment and materials
The core principle of the magnetic polisher is to drive stainless steel needles or abrasives to produce high-frequency motion through magnetic fields, and rub against the surface of the workpiece to achieve the polishing effect. However, workpieces of different materials (such as aluminum alloy, titanium alloy, copper, stainless steel, etc.) have very different requirements for parameters such as hardness, motion frequency, and magnetic field strength of the polishing medium. For example:
Aluminum alloy is relatively soft. If high-hardness abrasives or high-frequency magnetic fields are used, surface scratches may occur;
Hard alloys (such as tungsten steel) require higher energy input to achieve the desired effect.
Through sample testing, the surface roughness, dimensional accuracy, glossiness and other indicators of the workpiece after polishing can be directly observed to ensure that the equipment parameters match the material properties. A certain automobile parts manufacturer once purchased equipment directly without testing, resulting in batch scratches on the aluminum alloy shell after polishing, with a loss of more than 500,000 yuan.
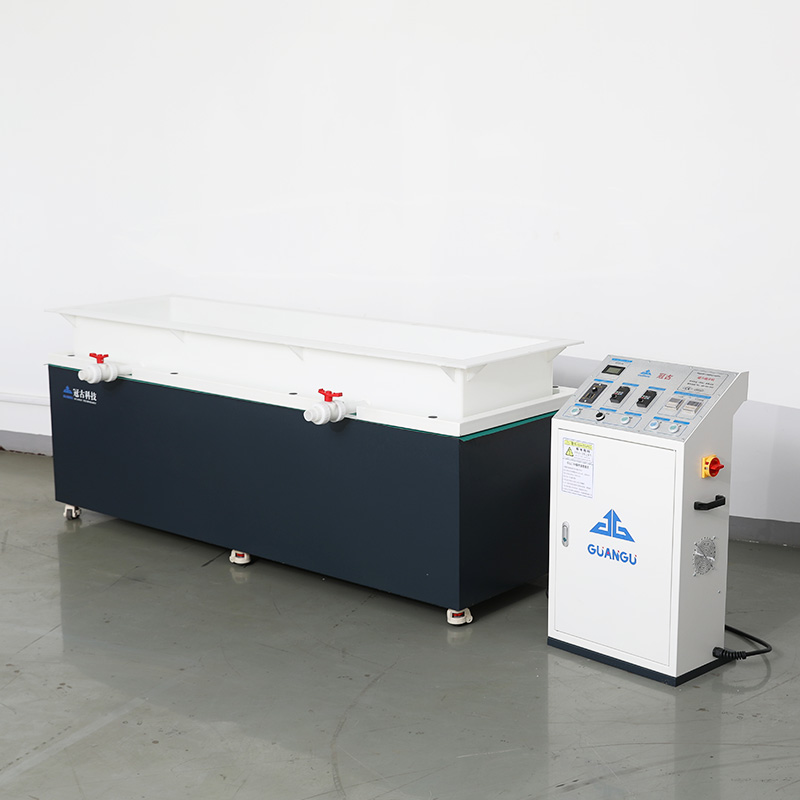
- Determine the optimal process parameters
The effect of the magnetic polishing machine is affected by many factors such as magnetic field frequency, abrasive ratio, processing time, and medium filling rate. For example:
Precision micro parts usually require high-frequency and low-amplitude modes to avoid deformation;
Large castings require extended processing time and coarse-grained abrasives.
By testing different parameter combinations, targeted process plans can be established. A medical device company found through sample testing that after adjusting the processing time from 30 minutes to 18 minutes and replacing ceramic abrasives, not only the efficiency was increased by 40%, but also the passivation layer of stainless steel surgical instruments was avoided.
- Evaluate the processing effect of complex structures
For workpieces with complex geometric shapes such as inner holes, threads, and deep grooves, whether the “no dead angle” advantage of the magnetic polishing machine can be fully utilized needs to be verified through actual testing. For example:
A watch company found through testing that gear shaft holes with a diameter of less than 0.5mm still have residual burrs under standard parameters, and special-shaped abrasives need to be customized;
A supplier of aerospace parts compared the workpieces before and after the test through 3D scanning, and confirmed that the inner wall roughness of the cooling channel with a depth-to-width ratio of 5:1 dropped from Ra3.2μm to Ra0.4μm.
Such data-based test results are the most direct decision-making basis for equipment selection.
- Avoid investment risks
The price of a medium-sized magnetic polishing machine is usually between 100,000 and 500,000 yuan. If it cannot meet the demand after purchase, it will lead to serious waste of resources. A hardware processing factory once purchased equipment without testing, and later found that its magnetic field strength was not enough to process steel plates with a thickness of more than 20mm, and the final equipment idle rate was as high as 70%. In contrast, pattern testing can expose potential problems in advance, such as:
Whether the maximum load of the equipment matches the production scale;
Whether the energy consumption meets the factory power supply standards;
Whether the noise and vibration exceed the workshop environment requirements.
- Optimize comprehensive costs
During the test, the processing cost of a single piece (including abrasive loss, power consumption, labor costs, etc.) can be quantified and evaluated. A jewelry processing company found through comparative testing:
Traditional drum polishing: cost per piece is 1.2 yuan, and the qualified rate is 85%;
Magnetic polishing: cost per piece is 0.8 yuan, and the qualified rate is increased to 98%.
In addition, the test can also help companies choose a more cost-effective abrasive type. For example, a company originally planned to purchase imported stainless steel needles (unit price 120 yuan/kg), but after the test, it switched to domestic ceramic composite abrasives (unit price 60 yuan/kg), achieving the same effect while saving 150,000 yuan in consumables per year.
- Verify equipment stability and maintenance requirements
Continuous operation tests can evaluate the long-term stability of equipment. In one case, the temperature of the magnetic field generator of a certain brand of equipment rose to 85°C after working continuously for 8 hours, resulting in a 12% decrease in polishing efficiency. Such problems are difficult to find in short-term demonstrations, but can be exposed through 72-hour sample tests.
- Feasibility verification of customized requirements
For special industries (such as semiconductor wafer carrier polishing), it may be necessary to customize magnetic field generators or develop special fixtures. A semiconductor company confirmed through sample testing that the supplier can develop a non-contact polishing solution for its 300mm diameter silicon wafer carrier to avoid particulate contamination caused by traditional mechanical contact.
- Evaluate the technical capabilities of suppliers
The testing process is essentially a touchstone for the technical strength of suppliers. High-quality suppliers will provide:
Multiple sets of alternative solutions;
Real-time data monitoring and reporting;
Process parameter optimization suggestions.
A German equipment manufacturer once conducted 20 sets of comparative tests for domestic customers, and finally increased the polishing pass rate from 89% to 99.5%. This in-depth service capability can only be demonstrated through actual testing.
Conclusion
Style testing is a key bridge connecting the theoretical performance of equipment with actual production needs. It can not only avoid procurement risks, but also establish a standardized process system for enterprises through scientific data accumulation. It is recommended that enterprises:
Provide representative typical workpieces;
Clearly quantify acceptance criteria (such as roughness, glossiness, tolerance range);
Require suppliers to provide complete test reports (including video records, test data, parameter recommendations).
Only through rigorous sample testing can we ensure that the magnetic polishing machine goes from “usable” to “easy to use” and truly becomes a production tool to enhance core competitiveness.
You must be logged in to post a comment.