Precision tool: the intelligent manufacturing revolution of small metal grinding and polishing machines
In the hardware industrial park in Yongkang, Zhejiang, a series of exquisitely shaped metal processing equipment are interpreting the precision aesthetics of modern manufacturing. These small grinding and polishing machines, known as “metal beauticians”, are reshaping the face of the traditional metal processing industry and becoming an indispensable intelligent manufacturing tool in the field of precision manufacturing.
Technological breakthroughs in micron-level precision
Modern small grinding and polishing machines adopt a modular design concept, increasing the spindle speed to more than 20,000 rpm, and with diamond grinding discs and intelligent pressure control systems, they can achieve a processing accuracy of ±2μm. After an aviation parts manufacturer introduced new equipment, the surface roughness of the turbine blades dropped from Ra0.8 to Ra0.1, and fuel efficiency increased by 5%. The vibration sensor and temperature compensation system equipped with the equipment can monitor the processing status in real time, automatically optimize the process parameters through machine learning algorithms, and improve the processing stability by 40%.
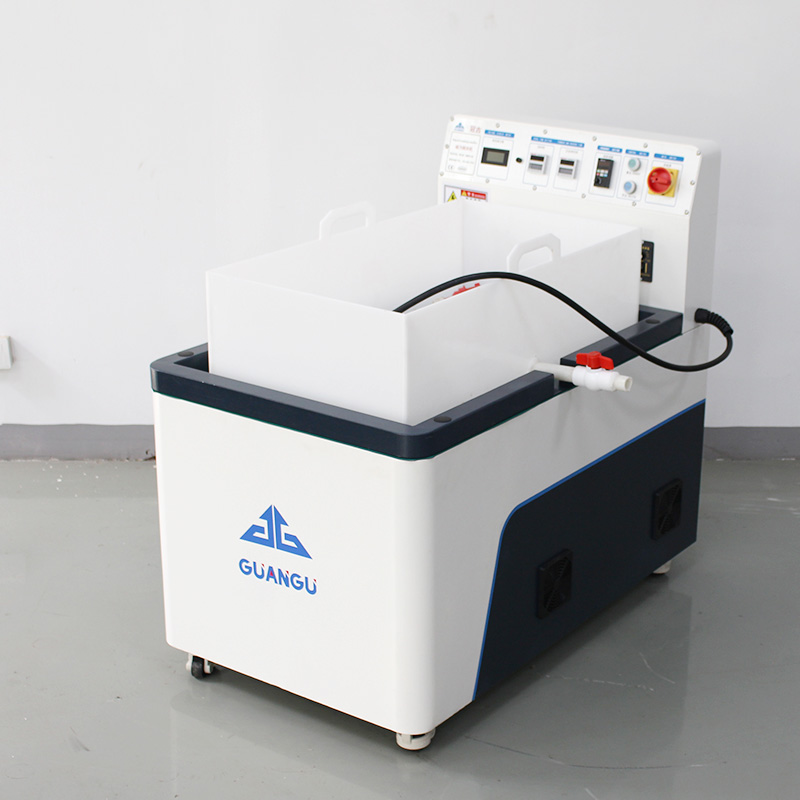
The scene revolution of flexible manufacturing
In the medical device manufacturing workshop, operators set the program through the touch screen, and the same equipment can complete the rough grinding, fine polishing and mirror processing of orthopedic implants. The modular fixture system supports 30-second rapid changeover, adapting to the diverse processing needs from micro dental instruments to large molds. After a watch company adopted the intelligent polishing system, the case processing time was shortened from 45 minutes to 12 minutes, and the yield rate jumped from 82% to 98.6%. The dust recovery device equipped with the equipment enables the air quality in the workshop to meet the ISO 14644-1 Class 7 standard.
III. The evolution of intelligent manufacturing
The latest generation of equipment integrates the industrial Internet of Things system and realizes remote operation and maintenance through the 5G module. The digital twin platform established by a company in Suzhou can monitor the operating status of equipment 200 kilometers away in real time, and predictive maintenance reduces the equipment downtime rate by 75%. The lightweight fuselage design using composite materials reduces the weight of the equipment by 35% compared with traditional models and reduces energy consumption by 28%. The adaptive polishing algorithm can automatically identify material properties, and the switching processing of 304 stainless steel and titanium alloy does not require manual intervention.
In the smart warehouse of Qingdao Port, the mobile polishing unit equipped with AGV is rewriting the traditional production process. These intelligent equipment groups work together through the MES system to build a flexible manufacturing unit. With the deep integration of AI vision and force control technology, small grinding and polishing machines are evolving from single processing equipment to the nerve endings of intelligent manufacturing, opening up new possibilities in the field of precision manufacturing. This intelligent manufacturing revolution triggered by micro-equipment is redefining the precision boundaries of metal processing.
You must be logged in to post a comment.